Delving into the intricate details of Cost Breakdown of Installing Fiber Cement Siding, this piece aims to captivate readers with a wealth of knowledge presented in a captivating manner, ensuring an enriching reading experience that is both informative and engaging.
Exploring the primary cost factors, labor costs, materials breakdown, and additional expenses involved in the installation process, this guide offers valuable insights for those considering this home improvement project.
Cost Factors of Fiber Cement Siding Installation
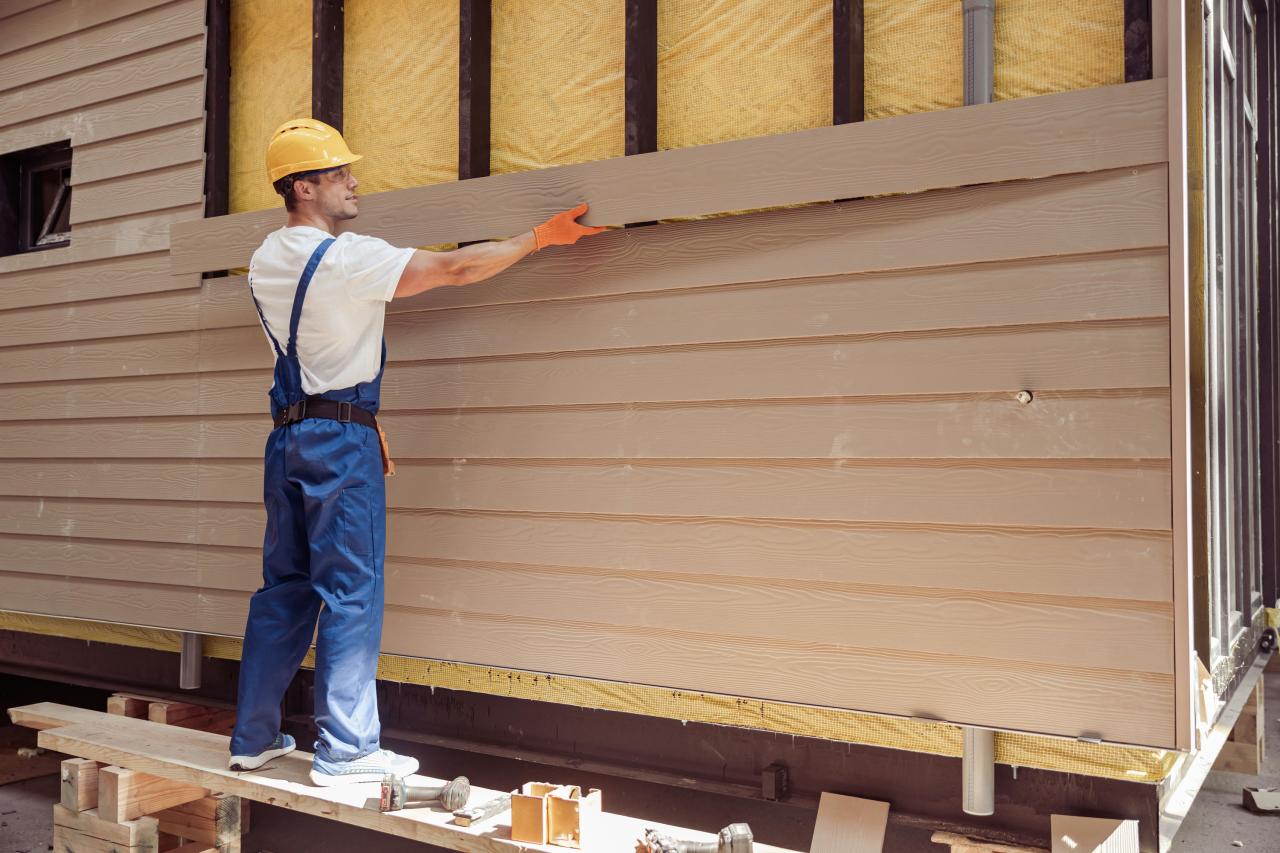
Installing fiber cement siding involves several cost factors that contribute to the overall expenses. These factors include labor costs, materials, additional expenses, project size, and installation complexity.
Labor Costs
Labor costs make up a significant portion of the total expenses for installing fiber cement siding. Skilled labor is required to properly install the siding, which can involve cutting, fitting, and securing the material to the exterior of the building.
The labor costs can vary depending on the experience and location of the contractors.
Materials
The cost of materials is another key factor in the installation of fiber cement siding. The siding itself can be expensive, especially if high-quality, durable materials are chosen. In addition to the siding panels, other materials such as fasteners, caulk, and paint may also be required, adding to the overall cost of the project.
Additional Expenses
In addition to labor and materials, there may be additional expenses associated with installing fiber cement siding. These can include permit fees, disposal of old siding materials, equipment rental, and any necessary repairs or modifications to the structure before installation can begin.
These extra costs should be factored into the overall budget for the project.
Project Size and Complexity
The size of the project and the complexity of the installation can also impact the total costs. Larger projects that require more materials and labor will naturally cost more than smaller ones. Similarly, projects that involve intricate designs, multiple stories, or challenging architectural features may require more time and expertise, increasing the overall expenses.
Labor Costs
When it comes to installing fiber cement siding, labor costs are a significant portion of the overall expenses. Hiring professionals to handle the installation can ensure a high-quality finish, but it comes at a price. On the other hand, opting for a DIY approach can potentially save money, but it requires time, effort, and a certain level of skill.
Typical Labor Costs
- On average, labor costs for fiber cement siding installation range from $4 to $8 per square foot.
- This cost includes the removal of old siding, preparation of the surface, actual installation of the fiber cement siding, and finishing touches.
- Additional costs may apply if there are complexities in the installation process, such as intricate designs or hard-to-reach areas.
Comparison: Professionals vs. DIY
- Hiring professionals for fiber cement siding installation ensures expertise and a quicker installation process, but it can cost more upfront.
- DIY installation can be more cost-effective, but it requires time, research, and the availability of necessary tools and equipment.
- Incorrect installation can lead to costly repairs in the future, making professional installation a safer choice for those unsure of their skills.
Factors Influencing Labor Costs
- Location: Labor costs can vary depending on the region, with urban areas typically charging higher rates compared to rural areas.
- Contractor Expertise: Experienced contractors may charge more for their services, but they can deliver superior results and complete the job efficiently.
- Seasonal Demand: Labor costs may fluctuate based on the demand for siding installation during peak seasons, such as spring and summer.
Materials Cost Breakdown
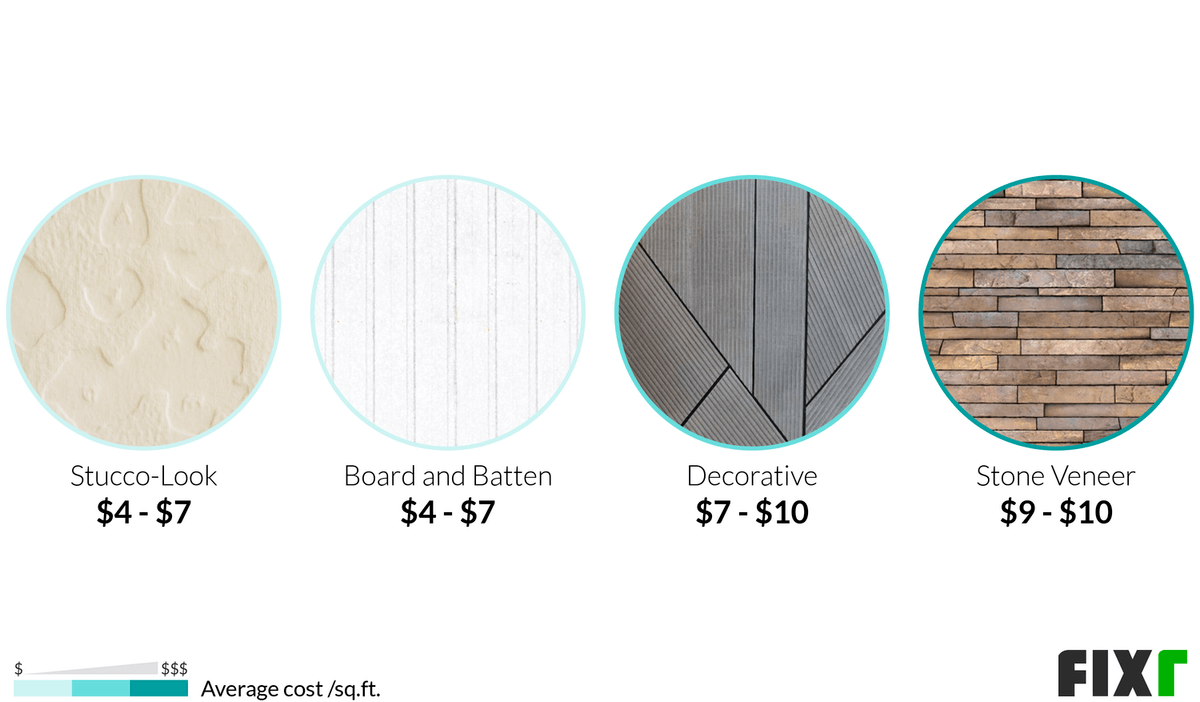
When it comes to the materials cost breakdown for fiber cement siding installation, it is essential to consider the quality of materials used as it directly impacts the overall expenses. Different types of fiber cement siding products also play a significant role in determining the material costs.
Quality of Materials
- The quality of fiber cement siding can vary greatly, with premium options costing more than standard or economy grades.
- Higher quality materials usually offer better durability, resistance to elements, and overall aesthetic appeal, but they come at a higher price point.
- Lower quality materials may be more budget-friendly initially, but they may require more frequent maintenance and replacement in the long run.
Types of Fiber Cement Siding Products
- There are various types of fiber cement siding products available, such as lap siding, shingles, panels, and trim boards.
- Each type of product comes with its own price range, with lap siding being one of the most common and affordable options.
- Shingles and panels may cost more due to their unique design and installation requirements, while trim boards are generally used for finishing touches and details.
Additional Expenses
When considering a fiber cement siding installation project, it's essential to account for potential additional expenses beyond just labor and materials. These extra costs can impact the overall budget and should be anticipated to avoid any financial surprises during the installation process.
Permit Fees
Permit fees are often required for construction projects, including siding installations. These fees can vary depending on your location and the scope of the project. It's crucial to check with your local building department to determine the necessary permits and associated costs.
Equipment Rental
In some cases, specialized equipment may be needed for the installation of fiber cement siding. Renting or purchasing this equipment can be an additional expense that should be factored into your budget. Equipment such as scaffolding, power tools, or safety gear may be necessary for a successful installation.
Waste Removal
Proper disposal of old siding and construction debris is another cost to consider. You may need to hire a waste removal service or rent a dumpster to handle the disposal of materials. Factoring in this expense ensures a clean and efficient work environment during the installation process.
Unexpected Repairs
During the installation of fiber cement siding, unexpected repairs or modifications to the structure of your home may arise. It's wise to set aside a contingency fund to cover any unforeseen issues that may arise during the project. This buffer can help prevent delays and keep your installation on track.
Finishing Touches
After the siding installation is complete, there may be additional finishing touches required, such as painting, caulking, or trim work. These final details can add to the overall cost of the project and should be included in your budget planning.
Consider the cost of paint, sealant, and any additional materials needed for a polished final appearance.
Conclusion
In conclusion, understanding the intricacies of the cost breakdown of fiber cement siding installation is essential for planning and budgeting effectively. By considering labor costs, material expenses, and potential additional costs, homeowners can embark on this project with confidence and financial foresight.
Query Resolution
What are the primary cost components involved in fiber cement siding installation?
The primary cost components include labor costs, materials, and additional expenses.
How do labor costs compare between hiring professionals and DIY installation?
Labor costs can vary significantly, with DIY installation generally being cheaper but requiring more time and effort.
What factors can influence labor costs in fiber cement siding installation?
Factors such as location, contractor expertise, and project complexity can impact labor costs.
How do different types of fiber cement siding products affect material expenses?
The quality and type of fiber cement siding products used can lead to price variations in material costs.
What are some tips for budgeting unforeseen costs during the installation process?
Anticipate additional expenses beyond labor and materials, and set aside a contingency budget to account for unexpected costs.